Industry 5.0 Implementation: Opportunity and Challenges in Global Market
April 04, 2024
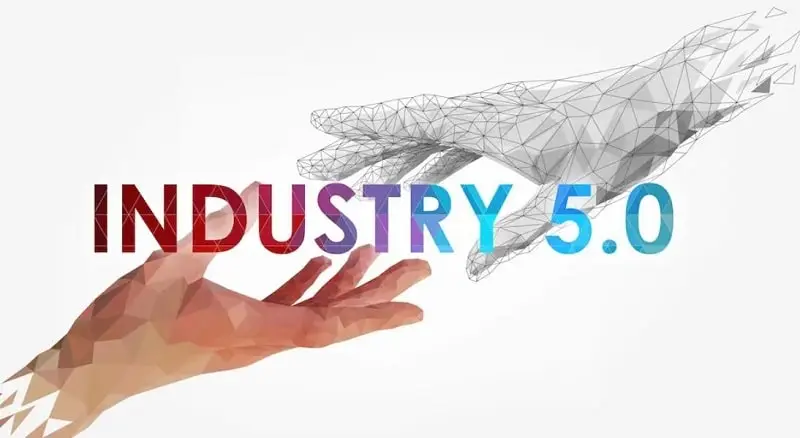
Introduction
Industry 5.0 represents a revolution where humans and machines collaborate to enhance production efficiency. Unlike in Industry 4.0 where the human element was somewhat sidelined, it now takes center stage. Human workers and robots will work alongside each other, boosting productivity in the manufacturing sector.
In this new era, the executive teams of manufacturing companies will play a crucial role in defining production lines, monitoring key performance indicators (KPIs), and ensuring smooth processes. The focus will be on fostering interaction and collaboration between humans and robots, with machine intelligence complementing human creativity.
The future belongs to robot manufacturers and industrial robots. With cutting-edge technologies such as artificial intelligence (AI) and cognitive computing, humans and robots are poised to revolutionize the manufacturing world, taking it to new levels of speed and efficiency.
Opportunities of Industry 5.0
Human-Machine Collaboration: In Industry 5.0, human-machine collaboration represents a fundamental shift from previous industrial revolutions. This collaboration focuses on integrating human skills like creativity, problem-solving, and decision-making with machine capabilities such as speed, accuracy, and scalability. By combining these strengths, companies can achieve new levels of productivity and efficiency. For example, in manufacturing, humans and machines can work together on complex tasks, with machines handling repetitive or physically demanding work, while humans oversee operations, make strategic decisions, and innovate processes. This collaboration not only increases efficiency but also opens up new opportunities for innovation and growth across various industries.
Efficient Resource Management: Industry 5.0 underscores the importance of sustainable practices and effective resource management, driven by advanced technologies like AI, IoT, and automation. These technologies enable companies to enhance resource utilization by providing real-time data monitoring and analysis, leading to more precise forecasting and planning. This results in decreased waste, lower energy consumption, and reduced environmental impact. For instance, smart sensors can monitor energy use and adjust settings automatically to improve efficiency, while predictive maintenance can minimize downtime and prolong equipment life. Overall, Industry 5.0 presents significant opportunities for companies to advance their environmental sustainability efforts while achieving cost savings and operational enhancements.
New Business Model: Industry 5.0 introduces new avenues for business models, notably servitization, where companies provide services alongside products, and outcome-based pricing. These models enable firms to stand out in the market and develop fresh revenue streams. Servitization, for instance, allows companies to offer maintenance, upgrades, or other value-added services, fostering long-term customer relationships and recurring revenue. Outcome-based pricing, on the other hand, aligns the success of the service with the customer's results, ensuring a mutual benefit. By embracing these innovative models, companies can differentiate themselves, enhance customer satisfaction, and drive sustainable growth in the dynamic business landscape of Industry 5.0.
Key Developments in Industry 5.0
- March 2024: Accel, a prominent venture capital firm, has unveiled the third cohort of its accelerator program, Atoms, which supports early-stage Indian startups. This cohort focuses on backing pre-seed ventures in the fields of Artificial Intelligence (AI) and Industry 5.0.
- January 2024: Siemens introduced groundbreaking innovations at the CES 2024 exhibition, the premier technology event, which merge the physical and digital realms to redefine reality. These advancements in AI and immersive engineering are aimed at creating the industrial metaverse, empowering innovators worldwide. Siemens showcased how these technologies are utilized through its open digital business platform, Siemens Xcelerator.
Challenges of Industry 5.0
Workforce Transition: The transition to Industry 5.0 demands a workforce with diverse skills, including digital literacy, problem-solving, and collaboration. This presents a substantial challenge for companies, as they must prepare employees to work alongside advanced technologies like AI and automation. Upskilling and reskilling programs are essential to close the skills gap and enable employees to effectively use these new technologies. Companies need to invest in training, reassess their hiring strategies, and promote a culture of continuous learning and adaptability to navigate the workforce transition in Industry 5.0 effectively.
Data Privacy and Security: The increased use of IoT devices and AI in Industry 5.0 has raised concerns regarding data privacy and security. Companies need to implement strong cybersecurity measures to protect sensitive information from breaches and cyber-attacks. This includes encryption, access controls, regular security audits, and employee training to raise awareness about potential threats. Compliance with data protection regulations such as GDPR and CCPA is also essential to ensure the lawful and ethical handling of personal data. Addressing these challenges is critical for building trust with customers and maintaining data integrity in Industry 5.0.
Regulatory Compliance: Industry 5.0 technologies often fall under complex regulatory frameworks, especially regarding data protection and safety standards. Ensuring compliance with these regulations can be challenging for businesses operating in multiple jurisdictions. It requires a deep understanding of the legal requirements in each region and the ability to adjust operations and technologies accordingly. This might entail implementing different compliance measures for each jurisdiction, which can be intricate and resource-intensive. Non-compliance can lead to legal penalties, damage to reputation, and loss of customer trust. Therefore, managing regulatory compliance in Industry 5.0 demands careful planning, legal expertise, and a commitment to maintaining the highest standards of data protection and safety.
Interoperability and Standardization: Industry 5.0 necessitates the integration of diverse technologies and systems, presenting challenges related to interoperability and standardization. The lack of common standards and protocols can hinder seamless integration and collaboration across different platforms and devices. Establishing interoperable systems is crucial for ensuring that different technologies can communicate and work together effectively. This requires industry-wide collaboration to develop and adopt common standards that enable different devices and systems to interoperate smoothly. Standardization efforts can streamline processes, reduce costs, and accelerate innovation by providing a framework for consistent and interoperable technologies.
How is Industry 5.0 Revolutionizing Business Strategies?
Combining Human and Technology
The fifth industrial revolution aims to enhance the digital transformation of businesses by integrating skilled workers with technology. This integration enables more meaningful and efficient collaboration in a secure environment. Essentially, it involves adding a human element to crucial technologies using new tools such as 3D printing, collaborative robots (cobots), smart systems, AI/ML, digital twins, blockchain, and more.
This revolution goes beyond mere technology. It's about leveraging the synergy between human beings and machines to forge new opportunities, unlock value, and propel growth. It entails fostering a culture that champions innovation, experimentation, and creativity, all while responsibly harnessing automation. Consequently, numerous organizations are starting to prioritize high-performance human-machine partnerships that facilitate greater automation throughout their business processes.
Investing in Employee Development
While industrial robots and artificial intelligence are automating many jobs, the impact is not solely negative. Instead of job losses, this automation is creating a demand for new skills and roles. For instance, according to The Future of Jobs Report 2020 by the World Economic Forum, industrial automation is expected to displace approximately 85 million workers but also create 97 million new jobs by 2025 across 26 countries.
This underscores the importance for companies to invest in the education and training of their workforce to successfully embrace and capitalize on this new wave of change. Industry 5.0 goes beyond automation and collaborative robots; it also involves creating fresh employment opportunities and ensuring that people remain central to the production process.
Honing in One Employee Engagement
Industry 5.0 presents numerous opportunities for companies to enhance their competitiveness, boost productivity, and cut costs while upholding people's rights – a concept the European Union refers to as the "people-centric" industrial revolution, emphasizing the importance of not neglecting individuals.
Companies embracing Industry 5.0 principles recognize that their most valuable asset is their people. They possess knowledge, expertise, and innovative ideas. They develop solutions, bring them to life, create from scratch, and innovate both individually and collectively. Organizations that adopt strategies to engage employees are more likely to retain key personnel and attract new talent, driving further growth.
The Three Pillars of Industry 5.0
Human-Centric Approach
In Industry 5.0, people are central to processes and decision-making. They actively participate in defining how things work, shaping the processes that govern their work, and comprehending the business's operations. They are not mere components of a machine but integral parts of a broader system.
Human-centricity is the foundational principle of Industry 5.0, a manufacturing approach in which technology empowers society to better serve human needs and be more human-centered. This shift marks a departure from the Industrial Revolution, where individuals were viewed as mere parts of a machine, easily replaceable commodities. In Industry 5.0, however, the human element is paramount. The focus is on understanding the workings of the human mind before designing systems for people to utilize.
Resilience
For Industry 5.0 companies striving to stay competitive in a constantly evolving environment marked by new technologies and changing market needs, the ability to swiftly adjust is paramount. This necessitates a rapid refocusing to stay ahead and adapt to market shifts, underscoring the importance of resilience.
Resilience involves bouncing back from setbacks, learning from failures, and maintaining a positive outlook despite challenges. It also entails ensuring that businesses have the necessary infrastructure to sustain high-level operations in the face of natural disasters or other crises. This resilience is closely aligned with sustainability, as it helps companies remain steadfast in pursuing their objectives despite external pressures.
Sustainability
Enabling employees to acquire new skills not only allows companies to cut costs while maintaining high-quality products and services, but also fosters greater employee loyalty. Providing opportunities for learning and career growth makes employees feel valued and appreciated, increasing their likelihood to remain with their employer. Employers who invest in lifelong learning for their employees often experience higher levels of engagement, productivity, and profitability. This benefits not only the companies themselves but also society as a whole, as a skilled workforce contributes to stronger communities with more opportunities for everyone.
Sustainability also involves implementing circular processes that promote the reuse, repurposing, and recycling of natural resources, thereby reducing waste and environmental harm. It encompasses optimizing energy management and improving manufacturing efficiency, all aimed at ensuring a better world for future generations. This underscores the importance of companies investing in people and processes that support a more sustainable future. Furthermore, companies should reconsider their metrics of success to align with societal values. Adopting new key performance indicators that measure human well-being and environmental impact is essential for creating a more sustainable future.
MD Mutahhir Furquan
MD Mutahhir Furquan, a graduate of the National Institute of Technology (NIT) with a bachelor's degree in Artificial Intelligence and Machine Learning, is well-equipped with the skills and knowledge needed to excel in the field. With a strong foundation in AI and ML concepts, he is poised to contribute significantly to the advancement of technology and innovation in various industries